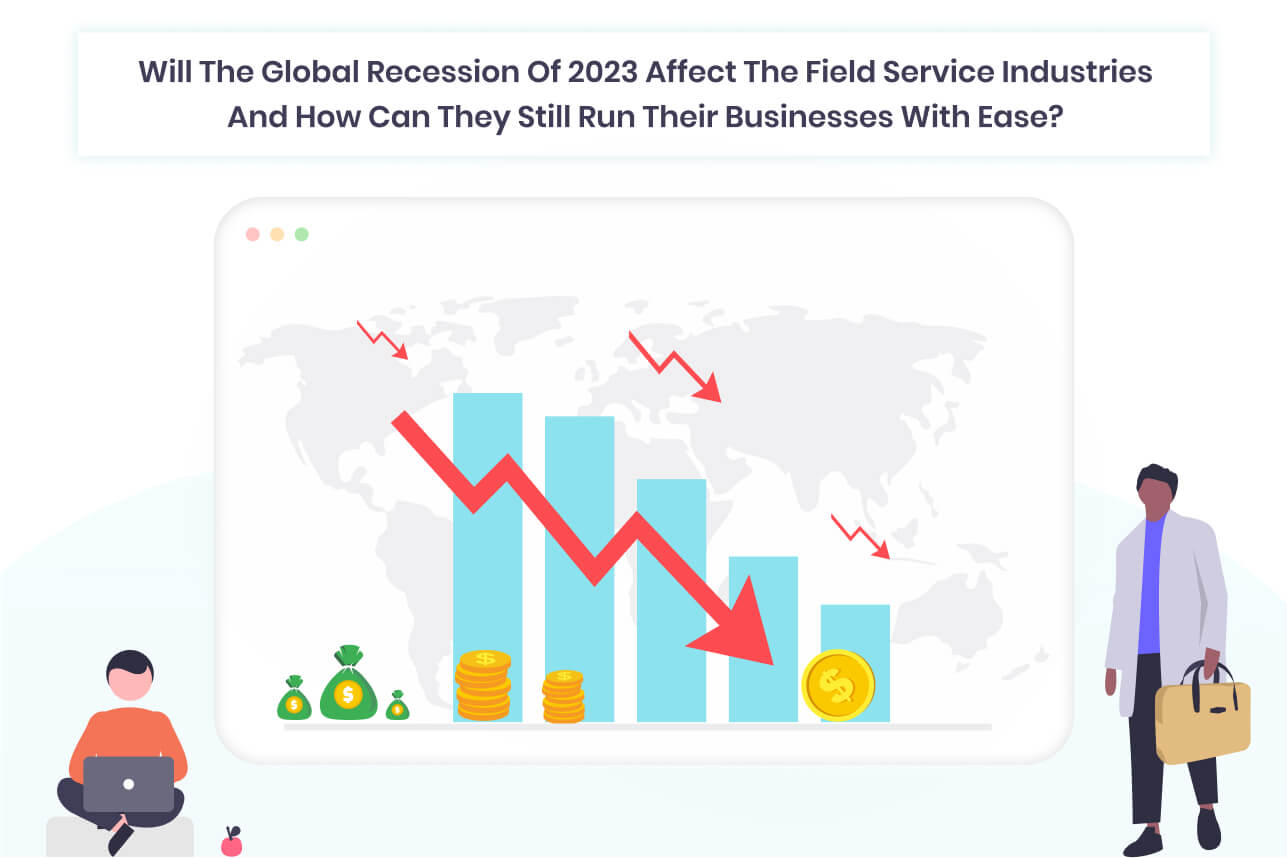
Any technique for keeping a company's equipment in excellent working order is referred to as equipment maintenance. It might involve both normal maintenance and remedial repairs. Mechanical assets, tools, large off-road vehicles, and computer systems are examples of equipment. The resources required to keep it all in excellent working order will differ depending on the type. Large construction equipment, for example, will have different repairs than automated food processing machines. .
Equipment maintenance is used in any industry that uses any type of equipment. The following are some notable examples:
Food Preparation: In the food processing business, heavy machinery, mobile equipment, and handheld tools all require maintenance.
Manufacturing of plastics: Plastics production plants utilize a variety of heavy and light equipment, all of which need routine maintenance.
Steel mills include: Steel fabrication facility maintenance employees look after everything from hot rollers and furnaces to portable tools.
Restaurants: To offer dependable service, there are many types of equipment used in commercial kitchens that must be kept in operating order. Restaurants can also stay in compliance with regulations if they repair their equipment on a regular basis.
Construction: The successful functioning of a construction firm depends on keeping heavy mobile equipment, portable power tools, and safety equipment in excellent working order.
Manufacturing of automobiles: Fabricating and assembling car parts need precision machinery. When that equipment is kept in good working order, production is at its peak.
Workshops: Workshops create a range of goods, such as woodworking, metal products, and blown glass, using a number of equipment. Given the industry's high standards, its equipment must be kept in tip-top shape.
Equipment management is a vital pillar for service-driven businesses that manage maintenance contracts for customer-owned equipment. As a result, this module is critical for warranty services such as labor or equipment.
Manage equipment maintenance at your clients' sites as efficiently as possible.
Equipment Management in EyeOnTask is built on top of the Service Management application's capabilities, which allows you to add new equipment, its address, nation, state, Brand, serial number, date of purchase, warranty, and much more...
Maintaining all details of equipment and products installed on your customers' files and facilitating them without any trouble is next to impossible. To keep track of warranties, serial numbers, default vendors, sale date, and installation date for each component equipment management are necessary.
Define preventative maintenance service order schedules and link them to recurring maintenance contracts or timetables.
Track warranty classes by equipment model to avoid overcharging customers for parts and labor when the service is covered under warranty.
You can access the routes from any device, at any time. All apps are web-based, allowing users with necessary privileges to access the system from any location on the planet.
For service-driven businesses that manage maintenance contracts for customer-owned equipment or own self businesses, equipment management is critical. This is especially important when it comes to equipment or labor warranties.
For service-driven businesses that manage maintenance contracts for customer-owned equipment or own self businesses, equipment management is critical. This is especially important when it comes to equipment or labor warranties. Let's discuss how EyeOnTask Equipment Management App makes it simpler for the business.
Easy tracking of equipment: The Equipment Management tool from EyeOnTask extends Service Management's capabilities by allowing you to trace the history of customer-owned or company-owned equipment. To minimize overcharging and complaints, provide warranty offers for equipment or components. It also keeps the numbers, default vendors, and sale and installation dates.
Error-free equipment management: You can track your equipment with EyeOnTask by selecting from a variety of categories. Many of the equipment, for example, are owned by construction or plumbing companies but operated by personnel can be easily listed. You can also keep an eye on any equipment that you own but it is being used at the client's location. EyeOnTask is an excellent tool for keeping track of such equipment
A reliable record-keeping system: Each equipment has its own record in the system, which field service workers can access via a mobile app. If technicians have the appropriate information, they can provide faster and higher-quality maintenance services for consumer equipment. You can create field service contracts to connect equipment for preventative maintenance for customers who visit frequently.
Click before and after service shots: Users of EyeOnTask can snap before and after service photos of their equipment. This function allows the user to check the equipment's condition before and after service or repair.
Custom Jobcard For Equipment: To offer users a satisfying experience EyeOnTask allows them to add custom fields for the equipment in the custom forms which can be later displayed on the JobCard and sent to the clients.
Unlike other equipment management services, EyeOnTask keeps the record of everything associated with equipment including supplier, photo, generate barcode, current status, type of authority (Owner or Service provider), date of manufacture, Warranty Expiry Date, equipment category, instrument cluster, date of manufacture, and every other details associated with it.
Barcode: As we know a barcode is a machine-readable representation of numerals and characters. EyeonTask offers its customers to generate barcodes for their equipment and save it for future uses. Also, it enables the customers to scan the barcode in order to get all the details about particular equipment.
Equipment Category: This is another exciting feature which is not generally offered by field management software. With Equipment Category features the customer/users can define a specific category according to their business. This eases down the searching process and streamline everything.
Equipment Group: Grouping of similar kinds of equipment simplifies the sorting process and users/customers can find their equipment easily. This feature saves a lot of time and energy and also keeps a clean record of all the equipment.
Customization: As EyeOnTask’s Equipment Management tools have everything in it, it also facilitates its users to add customized fields in order to make the equipment more detailed.
With EyeOnTask’s Equipment Management System, there is almost 0% probability of straying any equipment. This offers a single-screen platform to safely execute your business without any hassle.
Not only this, EyeOnTask always offers some additional perks. To manage equipment more efficiently, EyeOnTask introduced a feature to add tariffs on the equipment. With this feature the users can easily add tariffs to the equipment to different contracts and can change it at any point.
If you are looking for a one-stop solution for equipment management, contact EyeOnTask now! We are available 24/7 to assist you
Do you want to know more about features and prices call us on +13073164418 or mail me at support@eyeontask.com.